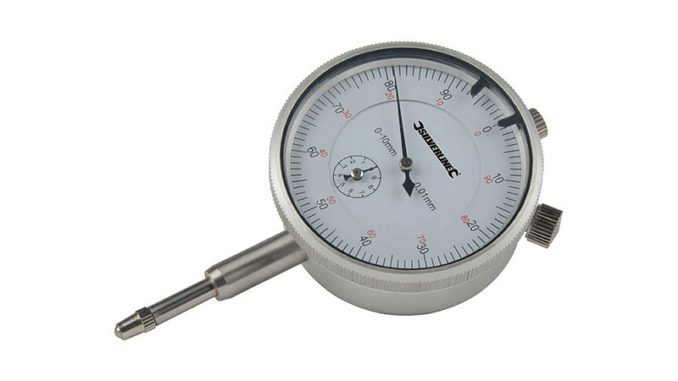
On m’a fait une rapide démonstration de son comparateur d’alésage cet été dans le but de contrôler l’état de mes cylindres. Le prix d’un tel appareil dans le commerce tourne autour des 400€.
Opérationnel, il est constitué d’un bras en bas duquel on trouve un doigt mobile. A l’opposé se monte un doigt fixe dont la longueur dépend du diamètre à mesurer. En partie haute du bras, un cadran gradué en 1/100e mm, va permettre la lecture des variation de diamètre sur la hauteur du cylindre. C’est donc bien un « comparateur » d’alésage.
Assemblage
Dans l’exemple qui suit pour apprendre à manipuler l’appareil, j’ai utilisé un bout de tube d’environ 55mm de diamètre intérieur. L’appareil se présente dans un coffret comportant de nombreux accessoires :
Le bras équipé du doigt mobile, le cadran.
![]() |
![]() |
![]() |
Des doigts fixes : on a le choix entre différentes tailles suivant le diamètre à contrôler (il en manquait certains dans la boite).
![]() |
![]() |
![]() |
Des bagues d’environ 1, 2 et 3mm, permettent de rallonger le doigt fixe au besoin.
![]() |
![]() |
![]() |
J’ai donc opté pour l’embout correspondant. La mesure est gravée dessus. Il est mis en place et immobilisé par un écrou moleté.
![]() |
![]() |
![]() |
![]() |
![]() |
Le cadran est mis en place et immobilisé grâce à un bouton moleté. La petite vis sert à bloquer l’aiguille, peut-être pour le transport ? Je ne l’ai pas utilisé. L’ensemble est prêt à servir.
![]() |
![]() |
![]() |
![]() |
Utilisation
Pour mesurer la cylindricité, lors de ce test j’ai réalisé deux séries de mesures croisées à 90°, chacune à 3 niveaux différents. La première série va permettre de comparer les diamètres à différentes hauteurs, la seconde de constater « l’ovalisation ».
Le dispositif assemblé est introduit et positionné dans le haut du tube.
![]() |
![]() |
![]() |
Il est incliné vers l’avant et vers l’arrière pour repérer la position sur le cadran de la mesure la plus élevée qui correspond à la coaxialité de l’appareil et du cylindre.
![]() |
![]() |
![]() |
![]() |
Etalonnage
Le zéro du cadran est aligné sur l’aiguille à cette position en tournant la bague moletée extérieure. On descend à mis hauteur du cylindre et on incline l’appareil vers l’avant puis vers l’arrière pour noter la mesure la plus élevée. On effectue un troisième relevé en position basse suivant le même processus.
![]() |
![]() |
![]() |
On peu en déduire que la surface n’est pas cylindrique mais plutôt conique. Le tube est déformé.
On procède alors à la seconde série de 3 mesures mais perpendiculairement au mesures précédentes et on note les résultats.
![]() |
![]() |
![]() |
On en déduit qu’il y a ovalisation de l’alésage.
Comment exploiter ces résultats :
Tout va dépendre des tolérances données par le constructeur. Dans cet exemple la première mesure d’étalonnage « zéro » correspond à un diamètre de 55,4mm. La côte maxi relevée étant donc de 55,82mm. Si les dimensions fonctionnelles du constructeur étaient 55mm +1/-1, pas de problème. Par contre si elles étaient 55mm +0.5/-0.5, on ne serait plus dans les normes.
Je suppose que dans le cas d’un cylindre moteur cela se traduirait par des pertes de compression et il faudrait sans passer à un diamètre de piston supérieur et réaléser en conséquence le cylindre (cas du XK2.8L) ou sa chemise (pour un 4.2L)
En vrai
Suivant les infos fournies, dans le cas d’un cylindre du bloc on optera pour deux séries de 4 mesures. La première des mesure qui va servir « d’étalonnage » du cadran s’effectuera sur la partie haute du cylindre, non usée par les segments. La suivante juste en dessous, une intermédiaire puis une en bas (au niveau du PMB). Ainsi, on aura une idée de l’usure du cylindre et de l’éventuelle nécessité d’un réalésage.
La première série en toute logique sera effectuée dans l’axe du bloc cylindres, la seconde perpendiculairement. Cette deuxième série risque de donner des mesures plus importantes conséquence de l’usure du cylindre par les segments suite aux efforts transversaux de la bielle lors de sa rotation à l’explosion (les pistons se déplacent légèrement en travers et non verticalement). Vu le sens de rotation du vilebrequin (le sens des aiguille d’une montre quand on est placé à l’AV, face au moteur , si j’ai tout compris c’est le flanc droit (tribord, RHD) des cylindres qui doit être le plus usé.
Suite à cette prise en main, je n’ai pu encore hélas réaliser les mesures sur mon moteur d’occase, car j’ai du rendre le matériel avant d’avoir fini de démonter mon vilebrequin, suite à un bête problème de tête de vis foirée sur le presse-étoupe AR. Ajouter à cela, un problème d’appareil photo… Mais le principe est là, et ce n’est que partie remise dès que ce sera possible…